Mechanical CAD (MCAD) software vendors are adapting to the demand for design processes that are more adaptable and conducive to teamwork and 3D design in manufacturing. This demand is encapsulated in what some call the three "A's" of modern design: agile development, augmented reality, and additive manufacturing.
Incorporating 3D design into these processes not only enhances the visual aspect of modeling but also significantly improves accuracy and efficiency, allowing for more complex and precise designs to be realized in a collaborative, digital environment.
Agile Development
Agile development is a software development approach that prioritizes incremental progress, continuous feedback, and team collaboration that is now being integrated into mechanical design. This integration involves segmenting extensive projects into smaller, more manageable components, enabling regular updates, and facilitating smooth cooperation throughout the design phase.
For decades, MCAD products have largely adhered to a one-user-one-part paradigm. However, vendors are now "tearing down walls" by introducing various in-software collaboration features. CAD software companies are devising strategies to match the collaborative versatility found in PTC Onshape, the sole native cloud-based MCAD design platform. Siemens NX, as an example, enables multiple users to monitor, follow, and manage modifications in real-time, with the option to narrowly focus tracking on a particular component or sub-assembly. Meanwhile, Dassault Systèmes' 3DEXPERIENCE platform serves as a unified hub for all team members to oversee and engage in projects, compatible with a range of Dassault engineering tools, including SolidWorks and Catia.
Augmented Reality
Virtual collaboration spaces, initially developed for the gaming industry, are now attracting attention in the manufacturing sector. Nvidia's Omniverse has emerged as a frontrunner, with its technology being adopted by Siemens Mobility, BMW, and Freyr, a Norwegian company specializing in transportation battery systems. These virtual environments can be accessed through traditional flat screens or through a range of "reality" headsets, offering an immersive 3D experience.
FREYR used Nvidia Omniverse and Siemens NX and Xcelerator to create an immersive view of the factory floor. There are 3D representations of the infrastructure, plant, machinery, equipment, human ergonomics, safety information, robots, automated guided vehicles, and detailed product simulations. Image source: Siemens.
MCAD tools are responsible for geometry, whereas simulation tools (CAE) are tasked with defining and testing physics. Software developers constantly enhance their products by exploring new ways to integrate CAD and CAE more closely. Many times, this results in design technology that favors AM. Such advancements encompass topology optimization, the generation of lattice structures, and the creation of printing supports to hold novel shapes in place until hardened. Additionally, the move towards early-stage simulation — applying simulation at the initial phases of the design process — further aids in optimizing designs for AM.
Autodesk Fusion 360 is one example that offers topology optimization within its comprehensive suite of integrated CAD, CAM, and CAE tools. Topology optimization enables designers and engineers to set specific design goals, constraints, and loading conditions for their 3D models. Utilizing these parameters, the software proposes the most efficient material layout within the designated design area, eliminating superfluous material without compromising the design's performance standards. Such a method is instrumental in developing designs that are both lightweight and material-efficient, proving particularly beneficial in sectors where minimizing weight and maximizing material use are paramount.
Autodesk Fusion 360 includes topology optimization routines that use artificial intelligence to return multiple design options for evaluation. These options are 3D printed prototypes for further evaluation. Image source: Autodesk.
Cognitive Design Systems, a French startup, is emerging as a noteworthy contender in the design for additive manufacturing (DfAM) space. This innovative software is capable of assessing the cost, feasibility, and environmental sustainability of 3D printed components. It leverages generative design technology and offers integration with collaborative platforms, including GrabCAD Print by Stratasys, enhancing its utility and connectivity within the DfAM ecosystem.
Cognitive Design Systems uses simulation and design for additive manufacturing processes to assess the cost, feasibility, and environmental sustainability of 3D printed components. Image source: CDS.
Additive Manufacturing
The first 3D printers on the market quickly became known in manufacturing as “rapid prototyping” machines. Today they have become much more. 3D printing, now known as additive manufacturing (AM), is a concept introduced by Jon Hirschtick, the co-founder of SolidWorks and Onshape, and is rapidly becoming accepted as the third primary method of industrial fabrication, along with formative and subtractive. For more about AM, read Cadalyst's series, "Additive Manufacturing 101."
One reason for the rapid growth of AM is that AM processes can sometimes accomplish what is otherwise impossible. For example, simulation software can confirm how oddly arranged channels improve cooling, yet such novel designs are either impossible to make with CNC or too expensive to make with formative methods. Enter AM, which can prove the design works. In fact, as technology continues to develop, a new genre of design exists — a subset of Design for Additive Manufacturing (DfAM) — just to create conformal cooling channels in injection molds.
AM is not the only innovation game in town. From the new hire in engineering to the CEO, everyone agrees product development and manufacturing needs to be more flexible and agile.
3D Design in Manufacturing
We stand at the forefront of a new era in manufacturing. The convergence of agile development, augmented reality, and additive manufacturing has gone from academic concepts to become a practical roadmap guiding unprecedented innovation and efficiency.
As MCAD software evolves to become more interconnected and user-friendly, it paves the way for a more collaborative and innovative approach to manufacturing. These advancements not only reflect the dynamic nature of the industry but also underscore the relentless pursuit of efficiency, precision, and sustainability.
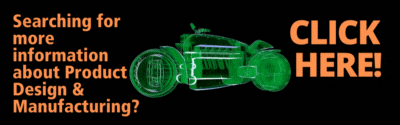
Searching for more information about Product Design & Manufacturing?
Click here!
Share This Post