CNC experts won't deny the fact that CAD software serves as an important tool while dealing with computer designing and manufacturing. After this step, we can leverage some of the outstanding specialized manufacturing and production techniques, such as CNC milling, injection molding, CNC turning, or 3D printing, to produce our initial design.
Here is a comprehensive guide focussing on how we can transition our product designs from the CAD drawing stage to CNC fabrication.
Image source: fomotek/stock.adobe.com.
Make CAD Files Ready for Real-time CNC Pricing
The cost of CNC is variable and frequently arbitrary. Manufacturers usually debate over the complexity of manufacturing a product. Before they manufacture it, none of them know what the exact final machining cost would be.
But nowadays, digital manufacturing solution providers harness AI-powered automation tools to provide real-time quotes. The ML (machine learning) algorithms can reliably project the cost of producing a part based on the order's data - part geometry, material, and volume.
Furthermore, when we integrate autonomous real-time costing with an AI-sourcing technology, the process gets even more streamlined for manufacturers to accept new orders. People send their designed products from CAD to manufacturing within a few minutes, and manufacturers can effectively utilize their production capacity.
Once we have optimized our CAD drawing for CNC fabrication, it's time to move forward.
Four Steps to Transform a Design From CAD Drawing to CNC Fabrication
1. Exporting the designed CAD file to a CNC-compatible format.
The initial step is to convert the CAD file into a format the CNC machine can understand. We may need to transform the drawing file into a G-code language. Nevertheless, one should prefer the STEP format (Standard for the Exchange of Product Data), the most widely recognized and compatible file format for CNC machines. It is a vendor-independent file format, and several CAD systems support it as an export format.
Alternatively, there is also the IGES (Initial Graphics Exchange Specification). It's an outdated format, and the problem with IGES files is that they're often larger than STEP files.
As a result, remember that our CAD designs must be transformed into STEP format at some point during the manufacturing phase. Exporting our drawings as STEP straight from the CAD system is a highly recommended approach. This way, we can analyze them before submission to ensure there are no conversion anomalies.
2. Creating the CNC technical drawing.
We should provide a technical drawing with every manufacturing order as it may contain crucial design information that a STEP file cannot read, such as if the CAD drawing includes:
-
Internal or external threads,
-
Several features with tolerances surpass the standards, or
-
Certain surfaces of the part have finishing requirements.
Even if the CAD model does not incorporate these elements, supplying a 2D drawing while placing a CNC fabrication order is often a great exercise. Numerous CNC vendors prefer technical drawings over 3D CAD files since they offer convenience in conveying the key dimensions, features, and essential attributes of a product.
They also make it simpler to analyze the efficacy of the machining processes employed during the production process. Also, in the event of disagreement, the producers use the technical drawing as the validation source.
Furthermore, it's pertinent to take a meticulous approach to the technical drawing. Consider adding sectional cutaways that illustrate the interior attributes if the part has concealed geometries. Make a note of the size and placement of all threads. Also, remember that the conventional tolerance will most likely be 0.125 millimeters. Thus any additional tolerances needing greater precision would need to be specified.
3. Collaborating with teams and stakeholders.
CAD models enable effective collaboration between the teams and stakeholders involved in that particular project. Apart from viewing a CAD file in its present version, authenticated customers can access the changelog and project timelines to get an update on the project completion state from the last time they reviewed it.
Also, prior to sending the CAD design to a CNC vendor, it's highly advisable to let all stakeholders access the most recent version and seek their approval. By doing so, we can establish and comply with standards and get their valuable inputs to avoid any discrepancies and anomalies later on.
4. Contacting CNC service providers to get a quote.
Nowadays, digital manufacturing platforms have made the process of procuring CNC production parts all the more streamlined than it has ever been. As we have already discussed, obtaining an instant/real-time quote needs just uploading the 3D files in a CNC-compatible format and providing the detailed specifications by selecting the material, volume, and processing time, as well as any other manufacturing requirements.
Also, here's a pro tip: if ordering the CNC-machined parts in bulk is an option from the project point of view, do so. This way, you can achieve CNC fabrication cost reduction on the overall budget.
Conclusion
It is not that challenging a process to prepare a CAD drawing ready for CNC fabrication. All we need to do is follow the above-discussed step-by-step procedure, and you can accomplish a successful project that complies with the budget without compromising on the final product performance and quality.
***
Viewpoint articles are tech-focused editorial written by experts from the CAD industry. This article was written by Vincent Hua from TSINFA.
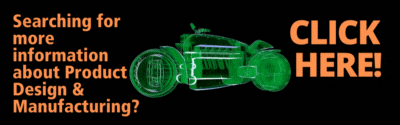
Searching for more information about Product Design & Manufacturing?
Click here!
Vincent Hua
Vincent Hua is the Marketing Manager at TSINFA (https://www.tsinfa.com/). He is passionate about helping people understand high-end and complex manufacturing processes. Besides writing and contributing his insights, Vincent is very keen on technological innovation that helps build highly precise and stable CNC Machinery.
View All Articles
Share This Post