Time-to-market (TTM) is everything in the design cycle. Designers need to keep moving the ready-for-sale date closer and closer. Now, with NX Mold Connect, mold makers can more easily collaborate with their OEM customers and vendors to make sure their designs are to spec and brought to completion quickly. To find out how, let’s peek into what happens at a typical mold manufacturing company.
Priority One: Speed to Market
Samantha, the supplier, is a salesperson in a mold manufacturing company. She has just left a meeting with Oscar, the OEM, a CAD designer who works for her customer. He let her know that her company will be receiving a request for quote to produce an injection mold for a case that will be used to package a new generation of power drills his company is developing. He has told Samantha that TTM is of the utmost priority to beat the competition, but he also wants to ensure that the molded case is cost effective and of high quality to showcase his product at point of sale. He wants to get high-quality, accurate quotations from his potential suppliers quickly so that they can award the job to the right supplier.
Injected Molded Case | Created in NX Mold Connect. Image source: Siemens.
During the initial meeting, Oscar’s design specs trigger a lengthy discussion about how the mold design and build should be executed. Oscar wants to avoid miscommunication between their respective teams, and suggests that everyone would be better informed and prepared for each stage of the process if he could relay his team’s engineering requirements to Samantha’s team in real-time using Siemens NX Mold Connect, a cloud-based SaaS (software-as-a-Service). He knows Samantha’s company already uses Siemens NX, and he knows integrating NX Mold Connect into their process would be seamless. To achieve the speed to market they need, using on-premise software and the old-ways of collaborating via email and file transfers, etc., will not work.
Samantha’s company understands that the future of collaborating on mold design and build is in the Cloud and has recently moved to using NX Cloud Connected - Mold Designer but has not used NX Mold Connect yet. Samantha is determined to win the job by delivering the quote quickly and, even more importantly, accurately, so they don’t lose money on the project.
Samantha reviews Oscar’s part design and right away begins assembling a list of the team members within her shop who will be directly involved in the mold design and build. She calls a meeting with them for an initial discussion and to brainstorm ideas about how the mold design for the case will develop based on the Oscar’s specifications. She also runs a design for manufacturing (DFM) analysis on the case design so that she can prepare an accurate bill of materials (BOM) using the tool costing feature in NX Mold Tools.
A visual BOM for the molded case. Image source: Siemens. Click image to enlarge.
For the mold designers and engineers on Samantha’s team, Siemens’ NX is a mainstay in mold design, and it has been for many years. Since making the move to the cloud, all design files from hundreds of mold builds have been moved from storage on a local server to the cloud, where they can be accessed from virtually anywhere at any time. In addition, they are stored securely, which is important to the customers who are wary about IP theft. Her company has invested thousands of dollars for the equipment and licenses required for the team to perform its design duties, plus NX is intuitive and easy to use.
Once an initial design concept for the mold is created, Samantha calls a virtual meeting with Oscar and brings her team in for added input during the design review. Unfortunately, Oscar’s team has changed some critical specifications for the case to accommodate cosmetic and functional changes in the drill designs. Samantha knows her drawings and her team’s corresponding BOM now will need revising, which is not unusual, but it will take more time to execute. In addition, it is imperative that the BOM is correct so that RFQs can be sent to suppliers of everything from the mold base and cavity/core inserts to electrodes, mold components, and mold finishing. All of this takes time and could cause them to miss Oscar’s delivery date, especially considering the current supply chain issues caused by the Covid-19 pandemic and global unrest.
Your BOM will automatically update. Image source: Siemens. Click image to enlarge.
Cloudy. . . With a Good Chance of Success
Samantha visits the Siemens website to find out more about NX Mold Connect. She is pleased to see that Oscar was right—it is a simple process to synchronize mold designs created locally using NX with the Cloud-based NX Mold Connect because she can subscribe and have her team up and running in minutes with instant-on access. There’s no need to arrange for a software representative to come to her company and install it — no waiting and no downtime! In the long run, it will be a tool that saves the company money. For example, her company currently pays a licensing fee of $775/month for the NX Cloud Connected - Mold Designer package and adding NX Mold Connect adds $250/month per user. But, with lowering TTM, Samantha believes her company can recoup this cost quickly, given the benefits that can be gained.
Welcome to NX Mold Connect.
Better RFQ Management. Oscar has communicated his wishes to work only with trusted suppliers on this project. NX Mold Connect makes it easier to manage and compare multiple RFQ’s sent out to different suppliers for the same part. Oscar can review trusted supplier databases and decide which vendors will be asked to quote the job.
Security. Samantha learns that there are multiple levels of security used by Siemens to ensure that all data is properly protected, including during the RFQ process. NX Mold Connect features a streamlined, in-app RFQ process by eliminating risky file transfers and email attachments. Plus, users can quickly and easily track RFQ status. Oscar notes that working in the Cloud speeds up the RFQ process by 35%, a strong selling point considering the time to market factor.
More Accurate Quotes. Cloud data storage provides suppliers with the very latest iterations of the product design because they are updated in real-time. There is a DFM feature that helps prove out design feature moldability to further ensure their quotes are on target. Using the advanced AI-powered Feature Recognition technology, it’s now possible for users to more accurately identify and quantify the critical features of the power drill design that can impact the cost of the tooling. Additionally, the Tool Costing function enables suppliers to then generate cost estimates based on the latest CAD drawings. Samantha shares these benefits with her boss, winning his enthusiastic approval.
In summary, while Samantha researches NX Mold Connect and gets her team up to speed on the app, Oscar updates the designs for the plastic parts for the case, and then submits the parts to Samantha to run the design for manufacturing analysis on the case to produce a DFM report. Samantha and Oscar begin collaborating in the Cloud using Siemens NX Mold Connect, satisfied that they now have a platform that provides interoperability with NX and the ability to connect securely to finalize the design and work together using the streamlined in-app RFQ process, DFM analysis tools, and tool-costing tools.
Samantha collaborates with mold engineers and designers on her team to generate the quote. All are working towards being awarded the job and the engineers on her team will create the mold design in NX Mold Design. Using NX Mold Connect to support the early supplier involvement and the RFQ process will speed up time to market and accelerate the actual tooling design performed by the Samantha’s team.
READ THE NEXT CHAPTER: What happens next? Find out more about this newly established level of collaboration using NX Mold Connect and how it can streamline the RFQ workflow, including keeping data synced, comparing RFQs, and more. READ MORE>>
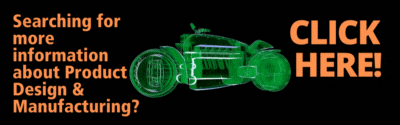
Searching for more information about Product Design & Manufacturing?
Click here!
Cynthia Kustush
Cynthia is the former senior editor of MoldMaking Technology Magazine. Currently she is a freelance author specializing in manufacturing, particularly for the metalworking and plastics industries. The daughter of a mold manufacturer, Cynthia “grew up in the trade,” and for many years has been actively involved in organizations such as the American Mold Builders Association (AMBA) and the Society of Plastics Engineers (SPE). She resides in Chicago’s western suburbs.
View All Articles
Share This Post