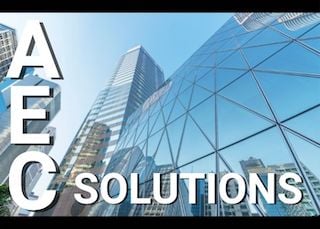
Collaboration between designers and builders in the AEC industry is bearing fruit in new and profound ways, via greater use of technology and data sharing. By more fully leveraging building information modeling (BIM) data, team members are sharing ideas earlier in project life cycles and shaping outcomes during all stages of projects, from design through construction and beyond. Owners are also reaping benefits, helping make informed decisions before projects go to construction, avoiding potentially costly change orders in the field.
General contractor DPR Construction has experienced numerous benefits of early collaboration through virtual design and construction (VDC). The company has combined BIM data with scheduling, sequencing, cost, and other data to essentially build projects digitally before physical construction. The approach has enabled the contractor to provide key feedback on project design and constructability.
Searching for more information about Architecture, Infrastructure, and Construction?
Click here!
“Leveraging data models allows us to be more collaborative with design partners and owners and ensure clarity on what the end project result needs to be,” said Hannu Lindberg, DPR’s national director of virtual design and construction. “The earlier we can get involved and start designing to a targeted budget, the less waste we generate.”
Merging Schedule and Design Information
Benefits of BIM collaboration often become apparent as DPR prepares schedules, construction sequencing plans, and cost estimates. Instead of simply estimating costs for a fixed design, the contractor can analyze multiple schemes and suggest design changes that aid construction.
“We leverage information the client has given us [in program documents],” said Chad Arthur, DPR’s northwest VDC leader. Using preliminary design data from design-build requests for proposals (RFPs) and other sources, DPR creates 3D cubes that represent functional building spaces, such as operating rooms in a hospital. Each cube can hold data related to that space and be moved around in scheduling and sequencing scenarios. “The ability to represent the functional space with a 3D object allows for more early massing and configuration,” said Arthur, referring to the development of a building’s general shape, form, and size. “Instead of detailing a couple of schemes, we can iterate 20-40 schemes.”
The ability to consider multiple construction scenarios helps DPR analyze parameters that impact costs, such as floor-to-skin ratios, as well as identify areas where vertical circulation is needed and where site impacts are most significant. “We can map information directly to an estimate, and format the estimate in a way that can be sorted by functional spaces,” said Arthur. This can help identify potential areas for cost savings before design is complete. “It eliminates the boom-bust cycle of documents” that requires multiple iterations to address budget overruns, he added.
On a Mid-Atlantic pediatric care facility project, DPR gained key insight by combining BIM and schedule data to optimize construction sequencing. “We were concerned with logistics,” said Roy Malcom, DPR’s central VDC leader. The project’s urban location limited available staging areas and required close coordination with the owner and local road authority. Steel erection controlled the project’s critical path, and sequencing the project’s two tower cranes was key to keeping the project on schedule. By using BIM data from an Autodesk Revit model and schedule data from a Primavera P6 schedule, DPR was able to color-code steel pieces by sequence and help trade partners understand what durations needed to be, Malcom noted.
Production report compares planned versus actual production to communicate progress and production with trade partners. Image source: DPR Construction. Click image to enlarge.
By leveraging BIM data, DPR was able to optimize crew sizes and make schedule adjustments to fit project needs. While traditional sequencing methods would rely on subjective determination of milestones, Malcolm explained, “The model took a lot of the subjectivity out of it and made it a single source of truth.”
DPR was also able to track construction progress against the project schedule and generate a dashboard to update team members on project status. The 500,000-square-foot facility, set to open in early 2023, is an addition to an existing hospital campus, so completion status is being watched closely by stakeholders.
Progress dashboard summary was used to communicate actual progress of concrete pours and steel erection. Image source: DPR Construction. Click image to enlarge.
Designers On Board
Early collaboration has also benefited project designers. While teaming with contractors in design-build and other arrangements requires workflow adjustments, the additional feedback results in improved designs, according to Jackie Lee, a project architect with SmithGroup, which has teamed with DPR on several projects.
“It’s been very enlightening,” said Lee. “It’s a bit of a paradigm shift, but we’re thinking about things earlier in the design process than we have before.” With contractors involved earlier and providing input during design, she says, “It’s much easier on the front end if we know what we’re designing to, rather than letting us design, giving us a price, and then asking us to redesign.”
Lee also sees BIM data aiding communication between designers, contractors, and owners. “We are all one team. It’s very inclusive. We are able to make design decisions that are more informed and quicker than usual.”
As an example of decision making, Lee cites selection of elevator equipment, where multiple options might be available. With digital collaboration, architects can provide more complete packages to owners and help the owner pick an option, she said. Previously they might gather information from other projects or vendors, but without contractor cost information. “Now we have additional layers of information that are more real,” said Lee.
SmithGroup also teamed with DPR on an ambulatory surgery center in central California. The 260,000-square-foot facility, planned for a late 2024 completion, is being developed under a progressive design-build contract, where the design-build team is selected early in the life of the project and then works with the owner to “progress” toward a final design and contract price.
During the selection phase of that project, the DPR team used preliminary BIM data to perform massing for multiple building schemes and present two schemes to the owner. The owner selection committee voted in real time at the final interview on the most important factors to consider and decided on one scheme. The model-based presentation was key to the team’s selection on the project, according to Arthur.
“Our message to the client was: ‘We’re going to make some decisions with you and we’re ready to hit the ground running on day one,” said Arthur. “We were able to do planning and programming through the model, then roll right into schematic design, which supports informed decision-making.”
Using preliminary BIM data, DPR presented two building schemes to a prospective owner during the selection phase. Image source: DPR Construction. Click image to enlarge.
Lessons Learned
Based on experience from previous projects, both DPR and SmithGroup see opportunities for leveraging BIM data more fully in the future. For contractor DPR, more up-front planning can help track progress more accurately, said Malcom. “When we jump to tracking progress without a good work plan, trends may look negative. In reality, we might be doing a decent job, we just didn’t have a realistic plan up front.”
Team alignment is also critical, added Malcom. “We need to make sure people are aligned and understand their roles in developing a model and design. It should happen together, not in silos.”
DPR’s Lindberg sees more forward-looking analytics aiding future project planning. “As we start integrating more information into the planning process, we’ll be able to do more predictive analytics and better trend forecasting. It’s about aggregating all the project information around the visual medium and using that as a means to understand priorities and make timely decisions,” he said.
Lindberg also foresees greater connection of cost components to BIM data. “We can look at not just production, but work in place in relation to cost,” he said. To increase the accuracy of performance tracking, contractors need additional data such as crew sizes and other subcontractor information in interoperable formats. “There are so many players in the sandbox and different systems. The more we can rally around a common platform, the easier it is to aggregate information,” Lindberg noted.
Malcom predicts new technologies being used to monitor progress and improve model-based workflows. Tools such as 360-degree photography, laser scanning, and drone surveys can be used to better understand construction progress. “We’re just scratching the surface in these areas,” he said. “We’re looking at how to get more autonomous methods in the field” for capturing data.
SmithGroup’s Lee sees a growing use of virtual reality and augmented reality in developing designs. “It allows clients to experience what a space looks like. Sometimes drawings can’t fully convey the design.”
Increased leveraging of BIM data appears to be a trend affecting all types of players in the AEC industry. The concept can also aid owners in operations after construction, as they use BIM data to monitor facilities and plan maintenance. And, collaboration appears to be key to making better use of the data, ultimately leading to improved designs and more successful, sustainable projects.