When Dr. Michael Grieves, Executive Director/Chief Scientist at Digital Twin Institute and expert on product lifecycle management, coined the term “digital twin” to describe a complete virtual version of a product, machine, or building, he envisioned service being a key use for the digital version. The digital twin would be populated with parts, assemblies, and process data before being built, and would guide both manufacturing and service.
Autodesk defines a digital twin for manufacturing as a virtual representation of a real-world product or asset “with the benefit of continuous, real-time data from the object.” The twin becomes both a reflective and real-time source of information “to help improve business practices, reduce downtime and increase ROI.”
Yet today most discussions around using digital twin technology have it backwards. Some companies create a digital version after manufacturing, as a record. Or, they create a model for simulation, but don’t connect it to the physical device. Yet, for those who have made the leap to digital twins, the resulting feedback loop provides valuable data for both service operations and future design upgrades.
The majority of product engineering projects create three distinct bills of materials (BOMs), the engineering BOM, the manufacturing BOM, and the service BOM. If the product is a small engine, the engineering BOM can show the engine as a single unit, but the service BOM must show all the distinct parts. Such granularity can be used to generate both As Built and As Maintained models. Additionally, the service BOM as a digital twin can keep track of product use, serial numbers of replaced parts, and more. The goal is to have constantly updated information that a tech in the field can use.
Autodesk is working on digital twin initiatives for both its Inventor and Fusion lines of MCAD software. Image source: Autodesk.
A Few Perspectives
One example is chemicals manufacturer BASF, which uses Autodesk Fusion for plant maintenance and Autodesk Inventor for plant design. Someone in the field can view Inventor data on a tablet, then compare it to the Fusion model. BASF also uses Microsoft Hololens to view the engineering data with augmented reality (AR) headgear, allowing a more holistic view.
This is not interoperability in the traditional sense of converting data from one format to another and sending it as a copy. The data is being used in its original format, providing insight without making static copies that start becoming outdated the moment they are created.
Another approach to practical digital twin technology comes from PTC, the company behind MCAD products Creo and Onshape. Creo Product Insight places sensors on the CAD model to act as the virtual equivalent of a physical sensor in the physical product. The virtual sensors are then given a connection to the physical product. PTC says connecting physical and digital instruments is the first step in creating a true digital twin. The connectivity between model and product impacts performance, behavior, and product use.
PTC also offers the ability to bring augmented reality into manufacturing and service. One PTC customer builds wind generation turbines; each unit is a custom configuration. By using an Internet of Things (IoT) connectedness as described above, PTC says the customer created an AR-based service guide that can overlay service instructions on the CAD data.
Siemens describes the digital twin as a technology for use in all five steps in the product value chain: product design, production planning, production engineering, production execution, and services. Thomas Hawn of Siemens adds that digital twin technology improves validation and commissioning, when it is used after engineering and before deployment. Once a product is deployed, data analytics drawn from a live digital twin can be used to predict divergent behavior (breakdown).
Ansys describes Twin Builder as a multi-technology platform that allows engineers to create simulation-based digital twins from manufactured using real-world or virtual sensor inputs as well as design data. Image source: Ansys.
Simulation and analysis specialist Ansys offers what it calls pervasive simulation, as part of its simulation-driven design initiative. Jacques Duysens, an Ansys business development specialist, says physics based simulation can be “the progenitor of digital twins.” He adds the goal is “to create virtual replicas of every physical asset in operation.”
Wrap Up
For small manufacturers, creating and using digital twins might seem a far off fantasy. Duysens cautions against such negative thinking and states,“Digital twins get a lot of talk. It is not magic, it is models.”
In relative terms, the price/performance of engineering software and the speed at which it can operate on new workstations is already transforming operations at larger manufacturing companies. As every aspect of creating and using digital twins becomes more democratized, these gains will soon reach affordability for even the smallest companies.
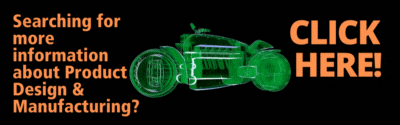
Searching for more information about Product Design & Manufacturing?
Click here!
Share This Post