Image source: DY/stock.adobe.com.
Technology advancements have always pushed the design and manufacturing industry forward, improving processes and end results. The past five or so years, however, have seen a level of advancement unlike anything we’ve seen before. Technology has brought engineers and manufacturing planners even closer together. This collaboration empowers teams to tackle complex challenges from almost anywhere, and at any time.
These advancements have forced many companies to change their approaches and push forward with digitally transforming every aspect of their operations. This is necessary just to keep up with their competitors and industry expectations. Teams responsible for designing, manufacturing, launching, and maintaining products are expected to make decisions at a pace not imaginable only a decade ago.
Transformation efforts often face significant obstacles due to outdated systems and entrenched processes. Companies struggle to foster collaboration, share accurate information, and establish strong, scalable processes.
Traditional Approaches, Historical Issues
Early iterations of product lifecycle management (PLM) software primarily revolved around mechanical designs and bills of material. These legacy PLM systems failed to move past those mechanical realms, neglecting diverse engineering disciplines such as systems, simulation, electronics, electrical, and software.
Traditionally, most enterprise engineering and design teams operated with departmental silos. They focused on individual design responsibilities rather than fostering cross-disciplinary optimization. This fragmented approach hinders innovation, especially in developing complex products. Such products require company-wide collaboration and integration. We must streamline processes, reduce redundancies, and enhance efficiency to drive higher quality and faster time-to-market.
The Need for a Unified Digital Thread
Interconnected data within digital information frameworks has never been more important. The need to provide teams with tools to locate, access, and leverage accurate digital information has become paramount. This is especially true given the distributed nature of organizations, teams, and data.
Establishing a consistent, robust digital thread is key to achieving full product lifecycle traceability across the entire organization. A strong digital thread will allow you to track a product and its digital assets all the way from concept through design, manufacturing, quality, and service. By fostering collaboration and streamlining communication, this interconnected framework expedites product development, drives tangible business outcomes, and promotes the collaboration and efficiency gains needed to stay ahead of the competition. It also makes it easier to respond to inquiries, demonstrate compliance, and adapt to evolving needs.
Achieving a proper digital thread requires bridging existing systems and closing legacy gaps, which is a formidable undertaking. This challenge is often exacerbated by the need to modernize entrenched systems and repositories as part of a digital transformation.
Establishing the Digital Thread
Getting started demands a nuanced approach. It should begin with a comprehensive evaluation of the existing technology landscape. Rather than adopting a one-size-fits-all solution, organizations should prioritize flexibility and interoperability. We all know that the technology landscape is constantly changing. Product requirements and consumer/end-user expectations are also evolving. Plan for change and embrace adaptability.
Approach the creation of a digital thread as an iterative process with incremental advancements, not a single overhaul. Analyze current processes and tools to identify inefficiencies and prioritize fixes. Embrace a phased approach to deliver value incrementally, mitigate risks, and expedite ROI.
Remember that a unified digital thread approach not only facilitates data exchange but also provides contextual insights essential for informed decision-making. As a part of the process, organizations should address any operational discrepancies and data inconsistencies before embracing solutions tailored to the organization's unique requirements.
The ultimate goal is to make accurate data and information available anytime, anywhere. A PLM-managed digital thread doesn't need to contain all data; it just needs to know how to find it. This approach ensures that the digital thread can provide a comprehensive and connected view of the product lifecycle.
Driving Future Innovation
Your digital thread approach should extend beyond historical and existing product information to foster a faster pace of innovation. The PLM platform connecting all product aspects today can also help engineers create new, innovative designs in the future. As new technology, like AI, becomes increasingly integral to product development, the importance of a digital thread cannot be overstated. AI relies on vast amounts of diverse data to generate accurate inferences and insights. A digital thread ensures seamless integration and accessibility of this data from various sources. It provides essential traceability, allowing for validation, compliance, and continuous improvement of AI algorithms.
Embracing a unified digital thread is not just a step forward – it's a game changer for digital transformation. It dismantles antiquated data silos, paving the way for enhanced collaboration, innovation, and operational excellence. By establishing this strong foundation, your organization will be well-equipped to seamlessly integrate new technologies and adapt to evolving end-user needs, ensuring sustained success in an ever-changing landscape.
***
Viewpoint articles are tech-focused editorial written by experts from the CAD industry. This article was written by Rob McAveney from Aras Corp.
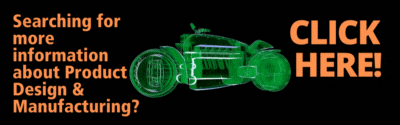
Searching for more information about Product Design & Manufacturing?
Click here!
Rob McAveney
Rob McAveney brings a lifelong passion for technology to the CTO role at Aras. For the past 20 years, he has focused that passion on building rich software platforms that solve difficult business problems for major industrial companies. Rob acts as Aras’ technology visionary and provides design oversight for future PLM technology, while remaining grounded in the realities of configuration management, systems integration, and the many other challenges of delivering enterprise software. Prior to Aras, Rob led technical sales engagements for Eigner, an early entrant in the PLM market. He began his career at Boeing, where he gained a broad understanding of engineering and manufacturing systems and processes.
View All Articles
Share This Post