Modern design software allows for multiple manufacturing choices. Engineers can choose subtractive manufacturing with advanced high-speed machining capabilities; additive manufacturing (3D printing), which builds complex geometries layer by layer; and established methods such as casting and injection molding that offer efficiency in mass production. The decision rests not only on part geometry but also on sophisticated software analysis that simulates, optimizes, and validates each approach.
Machining software (CAM) has evolved beyond simple toolpath generation into sophisticated decision-support systems. These platforms now analyze multiple factors simultaneously, helping engineers make informed choices between additive and subtractive approaches — or sometimes a combination of both.
Key to this decision-making process is the software's ability to evaluate part geometry in the context of manufacturing constraints. The system analyzes wall thicknesses, internal features, and required tolerances, automatically flagging areas that might prove challenging for traditional machining or require special considerations in additive processes. For instance, deep pockets that would require long, thin cutting tools in CNC machining might point toward an additive approach, while precise tolerance requirements might favor machining.
Software for computer aided machining can analyze complex part geometry to simplify the process of choosing a manufacturing method. Image source: PTC.
Production volume is also a critical factor. CAM software can calculate the crossover point where one method becomes more economical than the other, factoring in setup times, material costs, and machine utilization. Advanced simulation capabilities allow engineers to visualize the entire manufacturing process before committing to a method, identifying potential issues early in the planning stage.
Cost implications are automatically generated based on material usage calculations, estimated machine time, and tooling requirements. The software can compare the material removal rates of different cutting strategies against the build times and material usage of additive processes, providing clear cost metrics for each approach. These calculations extend beyond simple machine time to include factors such as material waste in subtractive processes or support structure requirements in additive manufacturing.
Subtractive Manufacturing Software Capabilities
MAN Energy Solutions, a global leader in marine and industrial equipment manufacturing, is putting contemporary subtractive manufacturing software to good use in their complex manufacturing processes. Faced with manufacturing high-value parts such as two-meter-long connection rods for marine engines, the company confronted a significant challenge: how to ensure reliable, efficient production while reducing manufacturing time to remain competitive.
By implementing advanced high-speed milling software from PTC, MAN Energy Solutions achieved remarkable results. The company says it reduced roughing operation times by 60% and cut overall manufacturing time by several weeks per part. Most importantly, the software enabled them to produce parts locally at costs that outperformed global competitors.
These efficiency gains come from several key software innovations. Advanced toolpath optimization algorithms constantly adjust cutting parameters based on real-time conditions. The software analyzes material engagement, adjusting feed rates and cutting depths to maintain optimal chip load while preventing tool overload. These adaptive strategies extend tool life while significantly reducing machining time. For MAN Energy Solutions, this meant eliminating costly rework and maximizing the value extracted from expensive raw materials.
Advanced high-speed milling software from PTC helped MAN Energy Solutions reduce roughing operation times by 60% and cut overall manufacturing time by several weeks per part. Image source: PTC.
Modern CAM software is also advancing the use of multi-axis machining strategies. It is now possible to automatically determine the optimal tool orientation for complex surfaces, and when to transition between 3-axis and 5-axis motion to maintain ideal cutting conditions. This capability is particularly crucial for parts with deep pockets or complex contours where tool accessibility would traditionally be challenging.
Real-time simulation capabilities allow for toolpath validation before reaching the shop floor. These simulations don't just check for collisions; they provide detailed analysis of surface finish quality, material removal rates, and potential tool deflection issues. For MAN Energy Solutions, where each raw part represents a significant investment, this simulation capability ensures first-time-right manufacturing.
Additive Manufacturing Software Innovation
The software driving additive manufacturing has evolved far beyond simple STL file preparation into sophisticated platforms that optimize both design and production parameters. These advanced systems now handle the entire additive workflow, from design optimization through build preparation and process simulation.
Design optimization tools are emerging as a significant advancement. Integrated lattice structure generation capabilities allow engineers to create parts that would be impossible to manufacture through traditional methods. The software automatically optimizes these structures for specific loading conditions while minimizing material usage. This optimization extends beyond simple weight reduction to include considerations such as thermal management and energy absorption characteristics — critical factors in industries like aerospace and automotive manufacturing.
Design for Additive Manufacturing software makes it possible to create novel designs that minimize weight, improve heat dissipation, or other critical attributes which can only be created using 3D printing. Image source: PTC.
Build preparation software has become increasingly sophisticated. Advanced algorithms analyze part orientation to minimize support structure requirements while optimizing surface quality and maintaining dimensional accuracy. Support structure generation has evolved from simple geometric patterns to sophisticated engineered structures that are easier to remove and use less material. The software can also automatically nest multiple parts within the build volume, optimizing 3D printer utilization while ensuring sufficient spacing for thermal management.
Print simulation capabilities now allow engineers to identify potential issues before starting a build. The software can predict thermal distortion, residual stress, and potential build failures by simulating the layer-by-layer construction process. These simulations consider factors such as heat accumulation, material properties, and support structure effectiveness, helping engineers adjust parameters to ensure successful builds.
Additive manufacturing software particularly shines when dealing with complex geometries that would be difficult or impossible to machine conventionally. Internal channels, organic shapes, and highly customized components can be optimized for the additive process while ensuring manufacturability. This capability makes additive manufacturing a viable option for applications requiring design freedom, such as conformal cooling channels in injection molds or patient-specific medical implants.
Integration and Hybrid Approaches
Advanced manufacturing platforms now offer unified interfaces where engineers can evaluate hybrid approaches. For instance, a part might be primarily produced through additive manufacturing for its complex internal features, but then finished with precision machining for critical tolerance surfaces. The software handles these transitions automatically, maintaining associativity throughout the process so that any design changes automatically update both the additive and subtractive toolpaths.
Looking forward, artificial intelligence and machine learning are beginning to play a larger role in manufacturing decision-making. AI agents, in particular, are a hot topic at the moment. Using these agents for real-time monitoring in-situ will make it possible to immediately compensate for defects or deviations. Such feedback could also be used to adjust process parameters dynamically.
These technologies analyze vast amounts of data to suggest optimal manufacturing strategies, and can quickly identify which features would benefit from additive versus subtractive approaches. For companies like MAN Energy Solutions, this points toward a future where software-driven manufacturing optimization can be applied across their entire product line, further improving efficiency and maintaining their competitive edge in the global market.
***
This month's MCAD column was sponsored by PTC. Thank you for your support.
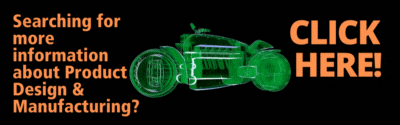
Searching for more information about Product Design & Manufacturing?
Click here!
Share This Post