One of the seminal movies of the 1960s was The Graduate, in which a new college graduate tries to navigate the challenges of love, social norms, and his place in a changing world. There is a line in which an older man at a cocktail party tells the young protagonist, “I want to say just one word to you: plastics. There’s a great future in plastics.”
Plastics made fortunes in the 1960s, and they are still revolutionizing manufacturing today. But, they aren’t alone. Thanks to the rise of additive manufacturing (AM), traditional materials are being re-invented for 3D printing. Polymers, alloys, composites, and ceramics are coming to market with a variety of improved properties including strength, durability, and thermal resistance. These new materials come with characteristics that surpass materials made for traditional fabrication methods.
Lattice structures can reduce material use in a part. Specific functional properties depend on the choice of material as well as geometric and mechanical design. Image source: Altair.
Many of these new materials are the foundation for innovation otherwise not possible. Silicone double networks, for example, are a new form of 3D-printable silicone that exhibit two separate crosslinking mechanisms that occur at different times. The unique properties allow for complex shapes to be created which exhibit exceptional mechanical properties and the ability to bond to a variety of other materials. Soft robotics, wearable devices, and biomedical models that mimic soft tissues are three most obvious applications.
With new materials come new AM methods. Electron beam melting has been used with metal for several years. The recent development of nanoscale eutectic composites makes possible the manufacture of high-strength, high-ductility products for high-temperature environments. (Eutectic materials are a mix of materials that, when combined, have a lower melting point than any of the constituent parts.)
So-called “smart materials” are coming to market that can change shape in response to external stimuli including temperature, moisture, or light. This will undoubtedly lead to the creation of new adaptive and responsive structures and products.
These new materials are also driving new ways to improve sustainability. “Circularity” is now a buzzword, describing a design philosophy of planning for eventual decommissioning and recycling of products.
New Materials, New Geometries, New Fabrications
The combination of new materials and new AM methods mean designers can create geometries that were previously either very difficult or impossible to manufacture with traditional subtractive or formative methods. Intricate lattice structures, internal channels, consolidated assemblies, and organic shapes (aka, biomimicry) all become possible.
Part consolidation can result in multiple benefits including the reduction of downstream welding and a reduction in jigs and fixtures. The blend of innovative material use and design for additive manufacturing makes such part consolidation possible. Image source: Altair.
Sometimes “new materials” does not mean “just invented,” it can also mean, “an existing material we never considered before.” One of the fundamentals of Design for Additive Manufacturing (DfAM) is the ability to consider the product across multiple axes of design. AM enables the use of a wide range of materials, including metals, plastics, ceramics, and composites. There is even a 3D printer for wood. A DfAM approach forces a broad comparison of material choices.
DfAM also allows for part consolidation and integration not possible with traditional manufacturing processes. Danish manufacturer Advansor specializes in equipment to help manufacturers reduce CO2 emissions. It found a pressure loss problem in a heat pump system. By leveraging DfAM methods and the use of CO2e Calculator from Danish AM Hub, Advansor redesigned the pump. Part count went from 17 to 3 and pressure loss was minimized. The new part offers a 1% energy savings. For a typical installation, this means an annual reduction of 19,400Kg of carbon dioxide emissions.
Not Just for Advanced Applications
The team of new AM processes and new materials offer unprecedented design freedom. It is easy to think these new possibilities are only for advanced applications like aerospace or nuclear fusion. Yet for every new type of robot or fancy space gizmo, there are hundreds of possibilities for “average” mechanical product development. Many of the new polymers, alloys, and composites are of reasonable cost. There are AM services available on every continent for companies not ready to invest in expensive new 3D printing equipment. The design freedom offered by AM and new materials — whether novel or “new to you” — can lead to innovations in cost of fabrication, performance, and circularity. The CAD and simulation tools in common use are up to the task. Now it is up to engineers to make it happen.
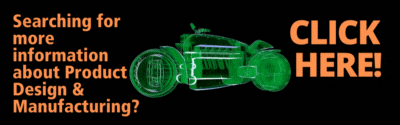
Searching for more information about Product Design & Manufacturing?
Click here!
Share This Post