DFM analysis, also known as design for manufacturing analysis, has become a critical step in the early stages of plastic product design. The advantages of performing a DFM analysis are many, including optimizing designs for more efficient manufacturing, speeding products to market, and reducing costs by eliminating later, expensive design changes in the tooling phase, which inevitably delays production.
In this next installment on Siemens NX Mold Connect, we check back in with Oscar and Samantha (OEM manufacturing customer and mold manufacturer salesperson respectively) and take a closer look at the tools they accessed within the browser-based app to perform more efficient DFM analyses for a new power drill housing, leading to a better part design and, hence, a better, more economical mold design and build. Readers will also discover how easy it is to use this app, even when the user is not a seasoned designer, allowing access to different roles within the company such as procurement, sales, and more.
Keep the Job Moving
Oscar, a design manager who also works in procurement for the OEM customer, has been working closely with Samantha, a lead salesperson for the mold manufacturer, who is not a mold designer but has working knowledge of Siemens NX. Since they began collaborating on the project in the cloud, communications about it have been streamlined, keeping all parties up to date on all aspects.
As Samantha began working with Oscar on the project, other work at her company was ramping up to a point where her designers had limited time to help analyze Oscar’s product design, a critical step in the RFQ process. At first, she was concerned because of her lack of experience using the NX Mold design tools. She consulted with her team to find out how to keep things rolling so as not to lose the job. Her engineers quickly reassured her that the DFM tools available in NX Mold Connect are so simple to use that even she can conduct a complete part design analysis herself.
DFM tools can be launched with one click in the NX Mold Connect app. Image source: Siemens.
User-Friendly DFM Tools Speed Results
With one click in the NX Mold Connect app, Samantha can launch the DFM tools, working in the cloud with the latest 3D iteration of the part design provided by Oscar. With these tools, she can:
Analyze Part Geometry. Samantha checks the drafts for non-drafted surfaces to make sure that the part can be cleanly ejected from the mold. She also checks for undercuts to see if any side actions, or slides, will be necessary for the mold, and determines whether there is another way to release the part without using slides, which would make the mold more economical to build. Part geometry analysis tool also lets her team see the cavity and core regions of the mold and assign undefined faces to define the parting line.
The app creates section views to give users deeper insight into the design. Image source: Siemens.
The app recommends any design revisions to make the mold easier and less expensive to manufacture. Plus, it creates section views to give customers insight and communicate the reason for any recommended design changes.
Copy Scene allows Samantha to capture the images with the design feedback to provide back to Oscar.
Samantha notes that the Feature Recognition tool in NX Mold Connect can help her identify undercuts and other aspects of a complex part design. For instance, ribs, bosses, and openings that will affect the mold design and build, and costs associated with it. Feature recognition can also be used to identify part information such as x, y, z dimensions, part volume, surface area, and minimum and maximum wall thickness. This functionality increases transparency and understanding of the mold requirements.
Users can easily perform wall thickness analysis. Image source: Siemens.
Analyze Wall Thickness. Within NX Mold Connect, Samantha has access to both the Ray method and the Rolling Ball (sphere) method for performing a wall thickness analysis. After choosing one of the options and applying it to the design, she simply adjusts the Results view so that she can quickly identify areas of the part that are either thinner or thicker than the values set by Oscar. It is also possible for her to probe thicknesses in certain critical areas and create callouts for design feedback to Oscar and her team of designers.
Mold Filling Advisor. Samantha knows that gate location is critical for filling the mold quickly and fully for every cycle to reduce material waste and produce perfect parts. With material costs at a premium today, using the Mold Filling Advisor tool in NX Mold Connect gives her the ability to either select the gate location herself or have the app use its intelligence feature to pick optimal locations for the specified number of gates.
-
Within the Mold Filling Advisor, Samantha can select the material as specified by the OEM, find and select a supplier, and indicate the material grade. Results of the analysis are shown in three ways:
-
Length/Thickness Ratio: Simulates the material flow into the mold during the injection molding process, providing critical data about whether the part will properly fill with the plastic. Samantha can alert Oscar of any issues, allowing him to make design changes early in the design cycle, and preventing added time and expense in the quotation process.
-
Sink Marks: By revealing, early on, potential defects that may occur in the plastic part Samantha and Oscar can collaborate to improve the quality of the final product.
-
Cooling Time: With cycle times dictating profitability, results from this analysis help to ensure that the part will cool in the desired time to improve the efficiency of the manufacturing cycle.
The Results display within Mold Filling Advisor can be adjusted to make critical areas more visible by using the legend in the bottom righthand corner of the screen to help users detect any manufacturing issues early on.
Client Communication
After going through the DFM process using NX Mold Connect, Samantha gathers the data necessary to provide Oscar with a detailed report and recommendations for optimizing the design of the power drill housing. She knows he will appreciate revisions that make the mold easier and less expensive to manufacture. Using the Copy Scene feature in the app, she captures images from the analysis that help illustrate to her customer the aspects of the design to which her feedback pertains. In addition, she creates section views to give Oscar additional insights into any recommended design changes so that he understands why she made them.
With the entire product DFM process conducted in the cloud, Samantha knows her report will be accessible by Oscar instantaneously, once she alerts him. In turn, her design team will also have instant access once the customer reviews and signs off on the recommendations — a streamlined process that previously they had not experienced.
Design for manufacturing tools in NX Mold Connect have been a game changer by taking the quotation process to the next level. Users, even those who are less experienced, now have the tools they need to fully understand the geometry of the plastic part they are working with and ensure that the downstream tool costing calculations are efficient and do not require rework.
Start at the beginning and read Oscar and Samantha's mold design success story.
READ THE NEXT CHAPTER: Stay tuned for more on this newly established level of collaboration using NX Mold Connect and how it can streamline the RFQ workflow, including keeping data synced, comparing RFQs, and more. In the next installment, we find out how Samantha uses NX Mold Connect to gather estimates from suppliers so she can feel confident in her build estimates. READ MORE>>
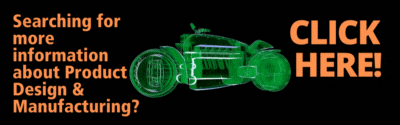
Searching for more information about Product Design & Manufacturing?
Click here!
Cynthia Kustush
Cynthia is the former senior editor of MoldMaking Technology Magazine. Currently she is a freelance author specializing in manufacturing, particularly for the metalworking and plastics industries. The daughter of a mold manufacturer, Cynthia “grew up in the trade,” and for many years has been actively involved in organizations such as the American Mold Builders Association (AMBA) and the Society of Plastics Engineers (SPE). She resides in Chicago’s western suburbs.
View All Articles
Share This Post