For a generation, 2D CAD drawings drove the manufacturing process. The drawings always came in sets, delivering not just designs but orthogonal projections, geometric dimensioning and tolerancing, BOM data, and much more. The workflow was the electronic equivalent of manually produced design data.
As solid modeling in 3D became common, many companies added a layer of complexity: design in 3D, communicate in 2D.
Model-based design is also commonly called model-based definition, because the model contains all the dimensioning and tolerancing information required for manufacturing. Image source: PTC. Click image to enlarge.
Design systems are now mature enough to unite all the data in those 2D sets within the 3D model. A new methodology, model-based design (MBD), also known as model based definition, can eliminate the extra steps required to create 2D sheet sets and separately communicate what is already found in the 3D model. Proponents of MBD say it offers immense benefits in time saved and accuracy maintained.
Nonetheless, traditional ways die slowly. For whatever reason, many companies are still in the 3D-to-2D paradigm. If your company is still sitting on the fence, thinking about updating, there are benefits you should know that go beyond the value of eliminating steps in the workflow.
Improving Product Quality
MBD simplifies applying tolerances. There is also complete certainty that tolerances are applied to the right feature. Anyone using this information can be certain they have up-to-date data so that GD&T, annotations, and PDI are always up to date. The cost and time of maintaining, distributing, and searching for all this product definition information is substantially reduced.
Reusing product definition information becomes easier when using a "3D Master" approach to MBD. The master model can be managed in PLM and then reused to make product families or future versions of the product. The complete part definition can be recycled into a new or revised product. Templates can be created from the model with specific tolerancing and annotations, to guide new areas of product development. The master model can also be used to create digital twins, expanding the utility and value of model data.
Holistic analysis of tolerances becomes possible in MBD, by using tolerance analysis tools that predict assembly variations. Build variation can also be simulated. One CAD vendor's research shows that running tolerance analysis and build variation simulation from the 3D model often makes it possible to loosen tolerances. This can lead to manufacturing cost reductions as great as 90%, depending on the situation.
Model-based design is not just for design work. Adjacent engineering tools including MATLAB from MathWorks supports the MBD workflow. Image source: MathWorks.
A Digital Golden Braid
MBD offers a compelling set of benefits. The value goes to another level when MBD is used along with two other significant design advances: generative design (GD) and simulation-driven design.
GD allows an engineer to review a mind-blowing number of design alternatives. Designers can quickly explore unconventional shapes optimized for specific criteria (weight, strength, heat dissipation, and more). The design options often go far beyond deep-rooted engineering assumptions, offering designs that are lighter, stronger, and more efficient than traditionally designed parts or products.
In addition, simulation tools are becoming more accessible and can be integrated early in the design process. Instead of waiting until a design is nearly complete, engineers can now run simulations on initial concepts or even on each iteration produced by generative design algorithms.
This early validation allows for rapid iteration. Engineers can refine concepts quickly based on performance data rather than intuition or assumption alone. By catching issues early and understanding performance trade-offs in real-time, development cycles can be significantly shortened, and product quality improved.
Model-based engineering supports simulation as part of design, such as this use of Creo Ansys Simulation and Creo Ansys Simulation Advanced. Image source PTC. Click image to enlarge.
From Coordinated to Connected
When generative design, simulation-drive design, and model-based definition converge, they create a powerful new paradigm for part and product development. The master 3D model continues to hold all the information. The company is able to advance from a "coordinated" information management model to a "connected" model.
The coordinated method provides the right information in the right context at the right time. On the other hand, this approach requires an understanding or agreement about what is needed and when it is needed. Detailed information is generally delivered in documents as part of a predefined process. If engineering data changes, new documents must be issued. Coordination and version control can quickly become complicated with back-and-forth exchanges putting a drag on productivity.
The connected method allows anyone with access permission to gather necessary data at will. Data sets are created directly from the master. These data sets are connected, and always stay current. The data can move in microapps, dashboards, and APIs instead of being locked up in a document.
MBD augmented by generative design and simulation streamlines communications between engineering, manufacturing, and quality assurance. It allows the supply chain to have insight into products. A connected manufacturing network can lay the foundation for new business models, new services, and new ways of becoming more innovative and efficient. It becomes easier to deal with new external demands such as sustainability.
The future of MCAD is not just about creating parts, it's about leveraging advanced algorithms and comprehensive 3D models to explore, optimize, and clearly communicate designs that push the boundaries of what's possible.
This new paradigm promises to enhance innovation, reduce time-to-market, and ultimately lead to better, more optimized products across industries.
***
This month's MCAD column was sponsored by PTC. Thank you for your support.
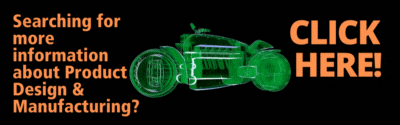
Searching for more information about Product Design & Manufacturing?
Click here!
Share This Post