In our first article, we explored some key benefits of digital transformation, and how it can lead to improved efficiency, increased profitability, and improved quality. In our second article, we introduced some of the technologies involved in digital transformation. In this article, we’ll dive deeper into how to leverage these technologies to achieve tangible benefits through digital transformation.
Image source: EmmaStock/stock.adobe.com.
Overview of Key Technologies
Our previous article mentioned several key technologies involved in digital transformation:
- Reality capture
- Digital twins
- Building information modeling (BIM)
- Artificial intelligence (AI)
Let’s look closer at how to leverage these technologies, and combine them in some cases, to create tangible benefits. After that, we’ll review other technologies that can be incorporated into digital transformation, such as virtual reality, automation, and 4D modeling.
With BIM software, such as Autodesk’s Revit, users can have a holistic view of a project and manage all the information for a built asset within BIM. Image source: Autodesk. Click image to enlarge.
Leveraging Digital Twins and BIM
While digital twins and BIM are two unique technologies, they are closely related and often complement each other. Let’s start by reviewing a couple of basic definitions:
- Digital twin: a digital model of a physical entity, ie., a building, facility, or region, that is updated with live or near real-time data.
- Building information modeling (BIM): the holistic process of creating and managing information for a built asset, integrating structured, multi-disciplinary data to produce a digital representation of an asset across its lifecycle.
By building digital replicas of physical assets, design professionals help owners and construction teams make more informed decisions. Working with realistic 3D models consisting of intelligent objects instead of simple lines, arcs, and other 2D entities, project teams can identify potential conflicts earlier in the building process and reap benefits throughout project lifecycles. Unified models provide better opportunities for collaboration, rather than working with a series of disparate CAD drawings unique to each discipline.
Expanding on the concept of 3D modeling, BIM integrates additional data beyond just geometric data to help owners manage assets across their lifecycles, from planning and design to construction and operations. In the building and manufacturing sectors, this often means moving from basic CAD software to Revit or other building software. In infrastructure and transportation work, products such as Civil 3D provide intelligent objects that can similarly be leveraged during and after construction.
Combining BIM with reality capture using a product such as this Leica scanner improves efficiency and productivity in the field and in the office, offering accurate review of buildings and the like. Image source IMAGINiT.
Combining BIM and Reality Capture Data
On their own, digital twins and BIM provide tremendous value, but they can provide even more value when married with other technologies, such as reality capture. By capturing existing conditions using LiDAR scanning or other imaging technologies, teams can overlay design information and current conditions to plan for the future. For example, owners can visualize how a new addition to a plant or a new breaker in a power substation fits in with existing facilities. Planners can determine whether certain equipment can be transported into available spaces with conventional means or if it will need to be lifted through the ceiling of the plant.
When projects proceed into construction, the combination of reality capture and digital twins continues to provide value. Plant startups are less likely to encounter surprises with the benefit of reality capture data. Accurately located existing facilities, such as piping and valves, simplify connection of new and old facilities.
Construction contractor Swinerton has found reality capture technology invaluable on building renovation projects. By obtaining laser scans of existing structures at the outset of projects, the company has saved significant time in compiling as-built information. “The laser scanners led to great improvements,” said Matt Zwetzig, Swinerton’s VD&C manager. “Measurements were gathered in a fraction of the time, teams knew they were working with accurate information, plans were created faster, correct parts were ordered the first time, and the parts fit as expected.”
O&M Value
Digital twins and BIM bring additional value as projects move into operations and maintenance (O&M) stages. The same model used during design can be used to track O&M processes. A pump or motor in a digital twin is more than just a shiny object, because it has data associated with it, such as specifications and maintenance records. Plant managers can track when replacement filters are required. They can readily access parts lists for certain equipment, and they can search for parts graphically by picking on a part and identifying it for replacement.
Sensors and IoT devices provide valuable links into downstream processes. For example, pressure and flow sensors can monitor pipe flow and identify potential problems, with graphic links in a digital twin model providing location data. Gauges can monitor fuel consumption of engines to assist with operational planning.
GIS Applications
Digital twins, BIM, and reality capture data can also be integrated with GIS data to provide value on an even larger scale. At a large midwestern university, this concept was applied to give university planners better visions of how to build out the campus. The combination of data has aided planning and design efforts on numerous projects, and will continue to do so for years to come.
Transportation projects can leverage intelligent data from Civil 3D models, such as underground piping that is often part of a larger network. Design and as-built information then becomes the system of record for utility companies, municipalities, or state DOTs and can be used for future planning and monitoring efforts.
AI-powered systems analyze data from sensors and historical records to identify potential safety hazards and risks on construction sites. Image source: IMAGINiT.
Artificial Intelligence
In addition to capturing the fancy of the general public, artificial intelligence (AI) has been increasingly providing practical applications to technology professionals. Building designers are using AI as a tool to develop multiple design options. Using large language models (LLMs), designers can enter key parameters such as square footage and space allocation and generate conceptual design options. With the AECO industry facing a workforce shortage, AI can provide relief by performing repetitive, mundane tasks, freeing professionals to do more critical, creative work.
In a similar manner, utilities can perform iterative design and analysis for future system upgrades. For example, when analyzing system capacity, a utility company can run different scenarios of ramping up capacity. With the US and other countries facing significant grid upgrade needs, technology can provide a much-needed aid in determining how to upgrade systems efficiently.
AI can also aid safety monitoring at work sites. Using a combination of digital models, sensors, and cameras, AI can help determine if workers are approaching unsafe working conditions or entering work zones that need additional safety measures.
Weather monitoring is another area that can benefit from AI. For example, AI-guided lightning protection methods have been developed that improve system reliability for construction sites, as well as buildings, neighborhoods, and regions. Wind, rain, temperature, and other weather parameters can also be monitored, with AI used to guide construction and other operations.
Other Technology
In addition to the technologies mentioned above, a variety of other technologies can be part of a digital transformation. Virtual reality (VR) and augmented reality (AR) aid design development and provide additional value during and after construction. Extending 3D modeling and visualizations to a new level, VR and AR allow users to actually experience the design environment interactively, navigating a model with VR headsets and other devices to perform design reviews and related tasks. During construction, VR/AR modeling can guide workers in a virtual environment to avoid safety hazards in the field. After construction, VR and AR can continue to guide facility owners with O&M work.
In another extension of 3D modeling, many professionals add the dimension of time to perform 4D modeling. By integrating construction schedules with 3D modeling, teams can better determine construction sequencing, material delivery, and other time-sensitive work. Taking the concept a step further, some firms are including cost parameters to perform 5D modeling.
Automation is another area that can aid digital transformation. By automating repetitive tasks through custom software, teams can save time throughout work processes and reduce touch points that require worker involvement. For example, if a 10-step BIM process can be reduced to five steps, teams gain efficiency and productivity.
Next Steps
If your organization is contemplating digital transformation, work with a qualified solutions provider to determine which technologies can most benefit your situation. A partner with industry experience is essential to introduce new technologies, update current systems, and analyze workflows to determine how to best incorporate new and updated technologies. While incorporating digital technologies may require some adjustments, IMAGINiT experts can help guide clients through the process to more fully leverage data, increase innovation, and improve collaboration, quality, and efficiency.
In our next article, we explore how to measure the benefits of digital transformation.
ARTICLE SPONSORED BY IMAGINiT Technologies.
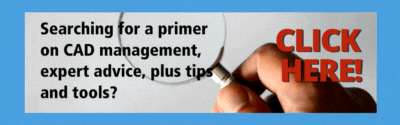
Share This Post